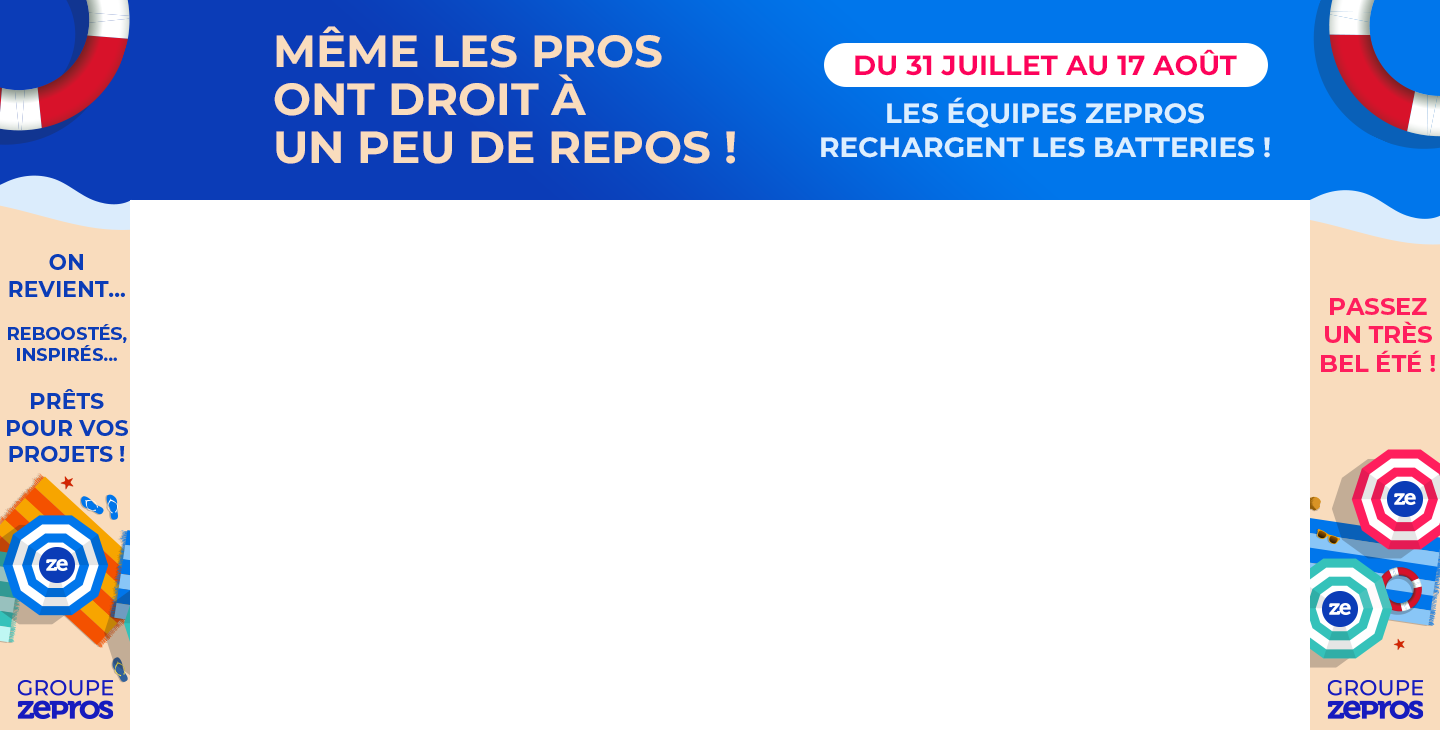
Xella s'appuie sur trois piliers : prescription, promotion et réseau

Le spécialiste du béton cellulaire ouvre les portes de son usine de Saint-Savin (38) où des investissements ont été réalisés pour accroître la sécurité des opérateurs, diminuer l’empreinte carbone des produits et incorporer toujours plus de matériau recyclé. Pour 2024, il compte s'appuyer sur la prescription et l'extension de son réseau d'entreprises expertes.
Les produits Ytong (gros œuvre) et Siporex (second œuvre, aménagement) sortent de cette usine d’une vallée verdoyante d’Isère. Propriété du groupe Xella, l’usine de Saint-Savin fonctionne depuis la fin des années 1980 et fait partie des trois unités de production de l’industriel dans l’Hexagone, avec celles de Saint-Saulve (59) et de Mios (33).
En tout, la filiale française qui alimente le marché national ainsi que l’Espagne, emploie environ 160 personnes pour un chiffre d’affaires de 57 M€. Ingrid Quantin, directrice marketing & commercial, explique : « Les investissements ont été réalisés dans ces sites de production plutôt que dans de nouveaux ».
Un peu plus de 1 M€ a été dépensé à Saint-Savin pour automatiser et sécuriser l’usine, qui tourne désormais six jours sur sept, au moyen d’une équipe très réduite : trois hommes sur la chaîne de production (coulage/sciage, autoclavage, stockage), un cariste et une personne pour assurer la maintenance des machines.
Rien ne se perd, tout se transforme
Sébastien Ray, le directeur des lieux, nous fait faire la visite : « Produire du béton cellulaire c’est comme produire un cake. On ajoute des ingrédients, sable, eau, chaux, ciment et agent d’expansion – qui sert de levure – dans un moule de 5 m3. Puis on le laisse reposer pendant une heure et demi, avant de le démouler, le découper puis de le faire cuire. Mais au lieu d’un four à haute température, nous utilisons des autoclaves à 11 bar et 180 °C pendant 10 heures ».
La recette semble simple, mais le procédé est délicat. Toute erreur de proportion ou de temps entraîne un rejet du produit final. Mais pas de souci, les chutes de production et autres produits endommagés ne finissent pas à la benne : ils sont broyés et réincorporés dans la chaîne.
Le concasseur permet d’obtenir de la poudre de sable, mais également du granulat, commercialisé en l’état (pour filtrat ou pour alléger les terres agricoles). De même, comme rien ne se perd, la vapeur des autoclaves est récupérée et valorisée afin d’économiser de l’énergie.
Fin 2024-début 2025, 0,4 M€ supplémentaire sera investi à Saint-Savin pour améliorer encore le criblage et le concassage, pour potentiellement incorporer non plus des rebuts de production mais des déchets de déconstruction.
Pour la matière première, l’implantation de l’usine n’a pas été faite au hasard. Elle est située à 500 mètres d’une carrière de sable de haute qualité, de silice très pur. En le broyant finement, Xella obtient une « boue de sable » qui sert de base à tous les produits en « béton cellulaire ».
« L’appellation est trompeuse, car ce n’est pas du béton, c’est un cristal de tobermorite (silicate de calcium hydraté) », nous révèle Sébastien Ray. À raison de 25 tonnes/heure, l’usine est alimentée en continu tandis que les moules suivent un ballet bien orchestré pour être enduits d’huile de décoffrage, remplis, stockés au repos avant d’être démoulés.
Les blocs obtenus, encore fragiles, sont découpés dans trois dimensions (longitudinal, horizontal puis vertical) par des fils d’acier tendus, afin d’obtenir les dimensions souhaitées (blocs, dalles, panneaux). Puis les éléments sont acheminés vers les étuves où ils prendront leur texture finale. L'usine de Saint-Sauvin produit quotidiennement 750 m3 de matériau de construction.
Une stratégie tournée vers la prescription
L’entreprise explique avoir remis la prescription au cœur de sa stratégie depuis le début de 2023. Grâce à un bureau d’études interne, elle propose des solutions pour toutes sortes de projets. Outre la tenue aux incendies du béton cellulaire, utile pour toutes les applications coupe-feu, Xella met en avant la performance thermique de son matériau qui permet des gains d’épaisseur et donc des mètres carrés habitables.
« Les projets sont optimisés en amont grâce à un variantage en béton cellulaire », nous apprend Arnaud Porte, directeur Technique & Développement pour Xella France. Malgré un marché 2024 compliqué, avec un segment de la maison individuelle en fort recul, l’industriel voit l’avenir avec sérénité, notamment grâce à de bons résultats en GSB (produits Siporex). Xella revendique une grande diversité des applications qui lui permettent de s’adapter aux évolutions, qu’il s’agisse de réhabilitation en collectif, de construction neuve en tertiaire ou de remise aux normes incendie.
En plus de ce pilier "Prescription", l’entreprise s’appuie également sur la force de son réseau Experts, qui regroupe 180 sociétés compétentes pour la mise en œuvre des solutions maison. Et Xella poursuit son travail avec la « promotion » et tous les négoces qui distribuent ses produits et permettent de recruter et fidéliser de nouvelles entreprises utilisatrices.
Le groupe entend fournir « des solutions constructives efficaces, durables et abordables ». Côté durabilité justement, il met en avant la réduction de ses émissions de CO2, déjà fortement engagée, et qui devrait encore diminuer d’ici à 2030 (-42 %), en optimisant les processus (ciment avec moins de clinker) et en revalorisant des déchets de déconstruction.
Pour y parvenir, Xella travaille avec l’éco-organisme Ecominero ainsi qu’avec le Syndicat des déconstructeurs-valorisateurs. Car l’important, comme souvent, est d’obtenir une matière première de qualité pour la transformer en matériau de premier choix.
Sur le même sujet
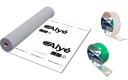
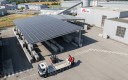
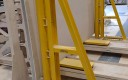
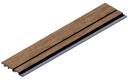